
Guidance
1. Benefits of assurance
“Assuring product inventory results” means making sure that the information about the number of products a company has is accurate and reliable.
Now, let’s look at the benefits:
- Increased confidence in reported information: If a company is sure that its inventory information is correct, it can have more confidence in using that information to set goals (like reducing inventory) and make important decisions.
- Enhanced internal accounting and reporting practices: This refers to improving the way a company keeps track of its inventory internally. Better methods of collecting data, calculating inventory, and reporting the information can lead to more efficient and accurate business practices. It also helps employees within the company to learn and share knowledge more easily.
- Increased confidence in results by other companies: If other companies rely on the inventory information of a particular product (maybe they are using it as a component in their own products), assuring the accuracy of the inventory results builds trust. They can be more confident that the information they’re using is reliable.
- Improved efficiency in subsequent inventory updates: Once a company establishes good practices for assuring inventory accuracy, it becomes easier and quicker to update inventory information in the future. This efficiency is beneficial when dealing with regular updates or when inventory needs to be assessed for other products.
- Greater stakeholder trust: Stakeholders include anyone with an interest in the company – customers, investors, employees, etc. If they can trust the reported inventory information, it builds confidence in the company’s overall transparency and reliability.
2. Key concepts in assurance
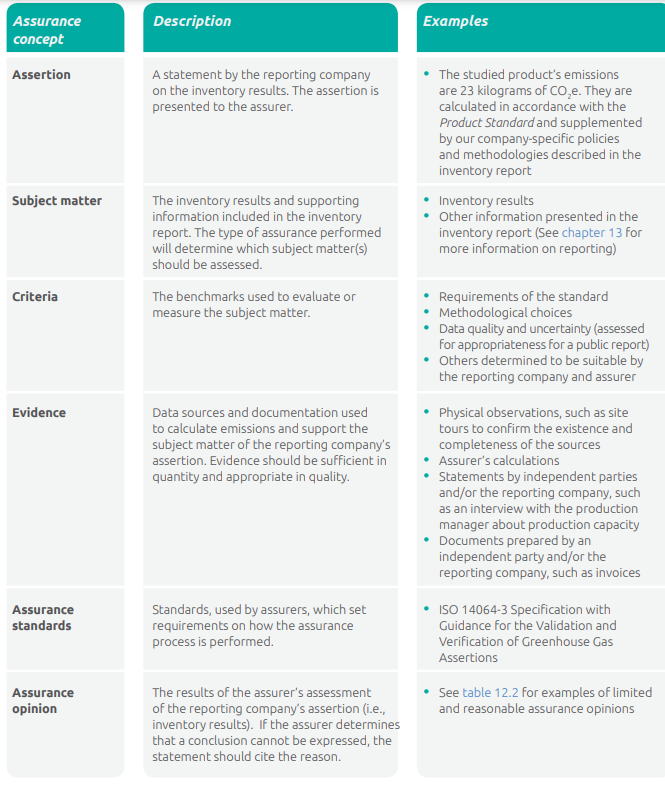
3. Materiality
- Material Misstatement: A material misstatement happens when there are significant mistakes, omissions, or misrepresentations in the Greenhouse Gas (GHG) inventory results. These errors are important because they could have a big impact on the results and might affect the decisions of the people using that information.
- Quantitative and Qualitative Aspects of Materiality: Materiality has two sides – quantitative and qualitative.
- Quantitative Materiality: This is about the numbers. It’s usually calculated as a percentage of the entire inventory or for each specific item in the inventory. When deciding what’s a significant mistake, those doing the assessment (assurers and the company reporting the inventory) consider the risk of a potential error and look at the history of previous mistakes. They might decide on a specific point (like a percentage) beyond which a mistake becomes significant.
- Qualitative Materiality: This is about the quality of the information. Even if a mistake doesn’t have a big numerical impact, it might still be important if it could affect the company’s emissions in the future or if it could mislead the people using the information.
- Uncertainty: Uncertainty is different from materiality. It’s not a known mistake; instead, it’s a measure of how well the data in the inventory represents the actual processes in the product inventory. In simple terms, it’s an indication of how sure we are about the accuracy of the information.
4. Preparing for assurance
- Why Prepare? Before this double-check (assurance) happens, the company needs to get everything ready. It’s like making sure all the necessary evidence and documents are easily available.
- What’s Needed? The type of evidence and documents that the double-checker (assurer) needs depends on what the company is talking about (subject matter), what industry it’s in, and what kind of double-check is happening.
- How to Keep Track? Keeping a plan (like a data management plan) helps the company organize and store all the information about their inventory process. This plan makes it easy to find the proof needed for the double-check.
- Before Assurance Starts:
- What the Company Should Have Ready:
- The company’s written statement about their inventory results.
- The completed data management plan.
- Access to enough proof (like invoices or bills of sale).
- Timing of Verification:
- When Does the Check Happen? The double-check (verification) is done before the company shows the public its inventory report. This is important because if there are big mistakes, they can be fixed before the report goes out.
- Why Start Early? The company should start this double-check early enough so that if there are problems, they can be fixed, and the inventory report can be improved.
- How Long Does It Take? The time it takes for this double-check depends on how complicated the inventory is and how sure the company wants to be about the information.
- Timing of Critical Review:
- When Does the Detailed Look Happen? Another type of check (critical review) can happen during the inventory process (while it’s still going on) or at the end.
- Why During? Checking during the process can catch and fix problems before the inventory is finished. It helps to avoid delays when the final report is published.
- Why at the End? Checking at the end allows the reviewers to look at the inventory results with fresh eyes. This is important for making sure everything is correct and makes sense.
- Being Fair and Independent: The people doing the detailed review need to be fair and not involved in making the inventory. Their findings should be based on the final report, and they should stay separate from the inventory development process during the detailed checks.
5. Assurance challenges
- Challenges in Assuring Product Inventories:
- Data Mix and Assumptions: Figuring out how much greenhouse gas a product produces involves using a mix of data and some educated guesses (assumptions). This mix can make things a bit tricky.
- Uncertainty in Inventories: There’s always some uncertainty, especially when it comes to emissions during the use of a product and what happens to it at the end of its life. This uncertainty can make the inventory (the list of emissions) less certain.
- Data Systems and Method Choices: It’s important to look at how data is collected and if the methods used are reliable. Assurance needs to check that everything is done in a trustworthy way.
- Data Mix and Assumptions: Figuring out how much greenhouse gas a product produces involves using a mix of data and some educated guesses (assumptions). This mix can make things a bit tricky.
- Challenges with Limited Control:
- Problem: Many sources of emissions are not directly under the control of the company reporting the emissions or the people checking (assurers).
- Three Ways to Deal with This:
- Change the Level of Assurance: Instead of promising to be very sure about everything (reasonable assurance), the company might say, “We’re pretty sure, but not super sure” (limited assurance).
- Switch to Critical Review: Instead of a deep, detailed check (verification), the company might go for a more general review (critical review). It’s like looking at the big picture without going into all the tiny details.
- Trust Another Assurer: If some emissions are coming from places the company can’t control, they might get another company to check those emissions. It’s like saying, “We can’t check these ourselves, but this other company says it’s okay.”
6. Assurance statement
The assurance statement conveys the assurer’s conclusion about the inventory results, and it may take different forms depending on whether the company is conducting critical review or verification, as well as if the assurance was performed by a first or third party. The required contents of an assurance statement are listed in the requirements section. An assurance statement should also include the following:
- Introduction
- A description of the studied product
- A reference to the reporting company’s assertion included in the inventory report
- Description of assurance process
- List of the assurance criteria
- Description of the reporting company’s and assurer’s responsibilities
- The assurance standard or type of critical review process used to perform the assurance
- A summary of the work performed
- The materiality threshold or benchmark, if set
- A description of the studied product
- Conclusion
- Any additional details regarding the assurer’s conclusion, including details regarding any exceptions noted or issues encountered in performing the assurance
- When there are material departures in the assertion from the assurance criteria, the reporting company should report the effect of the departures.
- Any additional details regarding the assurer’s conclusion, including details regarding any exceptions noted or issues encountered in performing the assurance