
Introduction
Accurate measurement of carbon dioxide (CO₂) emissions is crucial for regulatory compliance and climate initiatives. Two primary approaches are used in industry: direct measurement through Continuous Emissions Monitoring Systems (CEMS), and activity-based calculation methods using data like fuel consumption and emission factors. Below, we compare these methods, highlighting their accuracy, cost, real-time capabilities, treatment of biogenic carbon, and the challenges and innovations shaping their use.
Direct Measurement (CEMS)
Continuous Emissions Monitoring Systems (CEMS) measure CO₂ concentrations in flue gas and the exhaust gas flow rate continuously, often using in-stack or extractive gas analyzers and flow meters. This direct approach provides real-time emissions data, enabling immediate insight into operational performance or compliance status. CEMS can also simultaneously track multiple pollutants (e.g. CO₂, CO, NOx, SO₂) with suitable sensors, giving a comprehensive view of emissions at the stack.
A well-maintained CEMS offers the advantage of capturing actual emissions, including effects of incomplete combustion or abatement equipment, which activity-based calculations might miss. For example, a recent trial on marine engines found that direct CO₂ measurements were about 3.5% lower than the emissions calculated from fuel consumption, indicating the calculation method slightly overestimated emissions by assuming perfect combustion. In such cases, direct monitoring reflects real-world conditions (like unburned fuel or conversion to other compounds) more accurately.
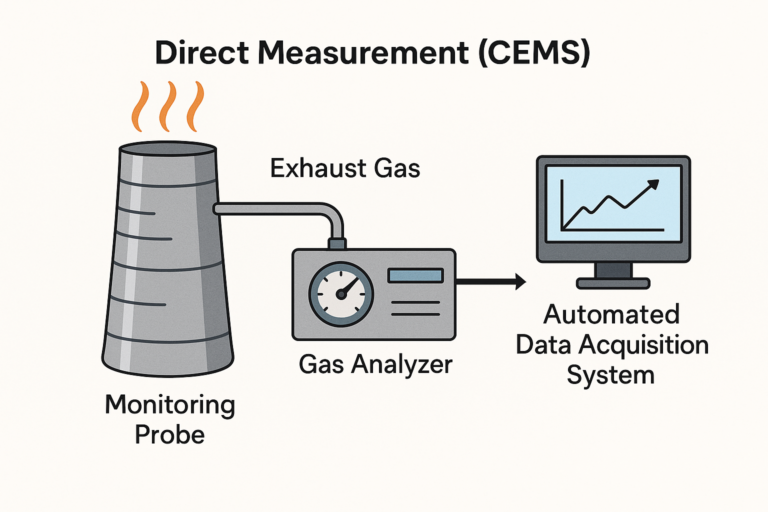
However, CEMS come with challenges. They involve significant capital cost and ongoing maintenance – gas analyzers and flow sensors must be installed on stacks and regularly calibrated and tested. Ensuring data accuracy requires rigorous quality control: periodic calibration with reference gases, linearity checks, and audits (such as EPA’s Relative Accuracy Test Audits). Another challenge is stratification of gas flow in large ducts or stacks. Exhaust gas is not always perfectly mixed; temperature or flow irregularities can cause CO₂ concentrations to vary across the stack cross-section. A single-point sampler might not capture a representative average, making accurate measurement difficult. Engineers address this by performing stratification tests and installing multiple sampling points or flow straighteners to ensure a representative measurement. Additionally, CEMS hardware can face downtime or drift, necessitating spare parts and expert oversight. These maintenance and reliability needs add to the operational cost and complexity of direct measurement.
Importantly, CEMS measure total CO₂ and cannot inherently distinguish biogenic vs. fossil CO₂. If a facility burns biomass along with fossil fuels, the CO₂ analyzer reports one combined stream. Accounting for biogenic carbon neutrality requires using fuel data to partition the measured CO₂. In fact, regulatory protocols note that when co-firing biomass, one must subtract the biogenic CO₂ portion from the CEMS readings and use a calculation method to estimate that biogenic fraction. Thus, even with direct measurement, supporting data on fuel composition is needed for accurate greenhouse gas accounting in mixed-fuel contexts
Activity‑Based Calculation Method
Activity-based methods estimate CO₂ emissions by calculating them from operational data. This typically involves tracking fuel consumption (or feedstock throughput, energy output, etc.) and multiplying by an emission factor or carbon content value for that fuel. For combustion sources, the calculation often uses the carbon content of fuel and an assumption of combustion efficiency to compute CO₂ output, sometimes adjusting for any carbon not oxidized to CO₂ (left as soot, CO, etc.). These methods are rooted in mass balance: essentially all carbon in the fuel will exit as CO₂ if fully burned, so measuring fuel use and composition yields a good estimate of CO₂ emissions.
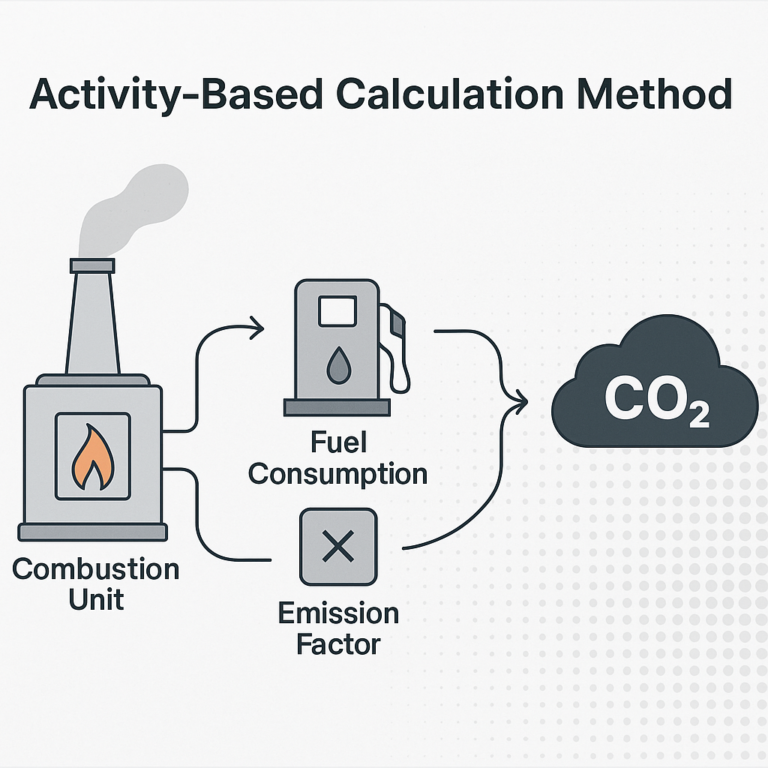
The advantages of calculation approaches include simplicity and low cost. No specialized stack instruments are required; instead, the focus is on fuel meters, utility bills, or production data and standard factors. Most facilities already track fuel usage for economics, so leveraging that data for emissions is straightforward. With high-quality data and proper factors, calculation methods can be quite accurate – in fact, under consistent conditions the results can closely match direct measurements. Studies have shown over 95% correlation between fuel-based CO₂ estimates and CEMS readings over extended periods. Accuracy depends on data quality: reliable fuel flow measurements and updated fuel carbon content values are critical. When those are in place, direct measurement is not necessarily more accurate than calculation. The Intergovernmental Panel on Climate Change (IPCC) and GHG Protocol note that, because of the strong relationship between fuel carbon and CO₂, CEMS rarely improves accuracy for CO₂ alone enough to justify its cost. As a result, many regulatory programs allow or even favor calculated CO₂ reporting for stationary sources, unless real-time data or multi-gas monitoring is specifically needed.
That said, activity-based calculations have limitations. They generally provide aggregated or periodic data rather than continuous real-time insight. Emissions are usually calculated hourly, daily, or monthly after gathering activity data, which may not capture short-term fluctuations. Also, default emission factors might not reflect specific operational efficiencies or fuel variations. If combustion is inefficient or control systems are in place (like carbon capture or flue gas recirculation), a simple calculation could overestimate actual emitted CO₂ (as seen in the 3.5% example above). Calculations must then be refined with correction factors for oxidation efficiency or use periodic direct measurements to calibrate them. Moreover, while calculation easily handles biogenic CO₂ accounting by segregating fuel types (one can apply separate emission factors for biofuel portions and report that CO₂ separately), it may miss unplanned emission sources (e.g. leaks, abnormal operating conditions) since it assumes all carbon goes through the intended combustion process.
Despite these caveats, the lower cost and ease of activity-based methods make them very popular. For many large plants, regulatory frameworks (like the U.S. EPA Acid Rain Program and the EU ETS) allow either CEMS or calculated methods. In practice, CEMS is often reserved for facilities that already must monitor pollutants like NOx/SO₂ or for very large emitters, while others use calculations with standard protocols
Comparison of CEMS vs Calculation
To summarize the differences, the table below compares key aspects of direct measurement (CEMS) versus activity-based calculation for CO₂ emissions:
Aspect | Direct Measurement (CEMS) | Activity-Based Calculation |
---|---|---|
Basis of Method | Measures actual stack gas concentration and flow to compute CO₂ mass emissions. | Computes CO₂ emissions from input data (fuel use, carbon content, etc.). |
Accuracy & Reliability | High accuracy if properly calibrated; captures real emissions including inefficiencies. Can be affected by instrument drift or stratification issues. | High accuracy with quality data; based on established emission factors. May miss nuances (incomplete combustion or abatement) but generally reliable. |
Cost & Complexity | Expensive to install and maintain (analyzers, flow meters, calibration systems). Requires expert maintenance and regular audits. | Low cost to implement; uses existing operational data. Fewer hardware requirements and minimal ongoing maintenance. |
Data Frequency | Continuous, real-time monitoring and instant readings. Ideal for operational control and immediate compliance checks. | Periodic or batch calculations (e.g. hourly, daily, or monthly) from logged data. Not inherently real-time without automation of data feeds. |
Multi-Gas Capability | Can directly measure multiple gases (CO₂, NOx, SO₂, etc.) simultaneously with appropriate sensors. | One calculation per pollutant; requires separate data (e.g. emission factors for each pollutant) rather than one integrated measurement. |
Biogenic CO₂ Handling | Measures total CO₂ only – cannot distinguish biogenic vs fossil CO₂. Additional calculations needed to identify biogenic fraction if biofuels are used. | Can explicitly calculate fossil and biogenic CO₂ separately by tracking fuel sources, enabling correct reporting of biogenic CO₂ (carbon-neutral) apart from fossil emissions. |
Operational Challenges | Needs frequent calibration and QA/QC checks (span, zero drift, interference tests) to maintain accuracy. Sensitive to probe placement and gas flow conditions. Potential downtime requires data substitution procedures. | Requires robust tracking of activity data and accurate fuel composition info. Susceptible to errors if data logs are incomplete or emission factors are outdated. Generally simpler to manage once set up. |
Use Cases | Preferred when real-time emissions data is needed or mandated (e.g. waste incinerators, large power plants, or when also monitoring pollutants like NOx). Ensures direct measurement for compliance. | Common for greenhouse gas inventories and compliance when continuous monitoring is not required. Used by many facilities for CO₂ reporting due to cost-effectiveness and accepted accuracy. |
Predictive Emissions Monitoring (PCEMS)
An innovative bridge between these two approaches is the Predictive Continuous Emissions Monitoring System (PCEMS), also known as PEMS. A PCEMS is a software-driven system that models emissions based on operational parameters rather than directly measuring the gas. Essentially, it uses a mathematical model trained on historical data or engineering principles to predict CO₂ (and other pollutant) emissions in real time. Key input parameters can include fuel flow rates, burner load, temperature, pressure, oxygen content, and other process variables that correlate with emissions. For instance, the UK’s environmental guidance describes PEMS as determining pollutant concentrations from the relationship with continuously monitored process parameters like fuel gas consumption and air-to-fuel ratio, combined with fuel quality data. These models can range from regression formulas to advanced machine learning algorithms that learn the plant’s behavior.
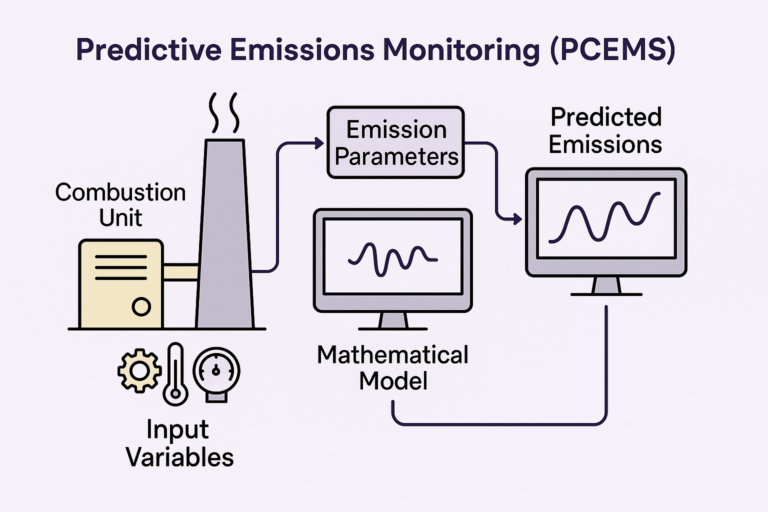
The appeal of PCEMS is that once a model is validated, it can provide real-time emissions estimates without the need for physical analyzers on the stack. This can significantly reduce costs and maintenance efforts. PCEMS are often used as an alternative or backup to CEMS – for example, if a sensor fails, the predictive system can temporarily fill in data, or in some cases regulators allow a certified PEMS to fully replace CEMS hardware. They are particularly useful when installing CEMS is impractical or for supplemental monitoring across multiple units. However, like any model, a PCEMS needs periodic validation (by comparing its predictions to actual measurements from periodic stack tests or a temporary reference analyzer) to ensure it remains accurate under changing conditions. It may also require retraining if the process or fuel characteristics change significantly. Despite these needs, PCEMS technology is rapidly maturing and is recognized in regulations (e.g. U.S. EPA’s Performance Specification 16 for PEMS) as a viable compliance tool.
Integrating Methods with Emitrix
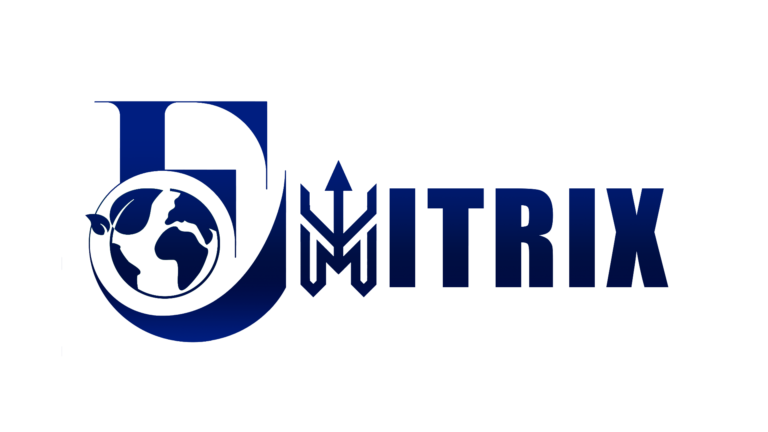
Whether using direct measurement, calculation, or predictive models, organizations increasingly seek to integrate multiple methodologies for a complete and flexible emissions management strategy. This is where platforms like Emitrix come into play. Emitrix is designed to enable seamless CO₂ emissions tracking by incorporating data from CEMS instruments, activity-based calculations, and even predictive models in one unified system. For example, an operator can feed real-time CEMS data into Emitrix for immediate monitoring, while simultaneously using the platform to calculate emissions for sources that lack CEMS (using fuel usage and standard factors). The platform can reconcile and visualize these data streams, providing a comprehensive emissions inventory that leverages the strengths of each method. Emitrix also supports the incorporation of PCEMS algorithms – ingesting live process sensor data and applying predictive models to estimate emissions continuously. By combining direct measurements with calculated estimates, Emitrix helps organizations ensure accuracy and fill gaps: CEMS data can be used to validate and adjust calculation models, and vice versa, all within one dashboard. This multi-method integration makes it easier to comply with reporting requirements, perform cross-checks, and gain insights into emissions performance without being tied to a single approach. In summary, Emitrix empowers companies to adopt a hybrid methodology for CO₂ monitoring, harnessing real-time data and reliable calculations together, and thereby enhancing confidence in their carbon reporting and reduction efforts.